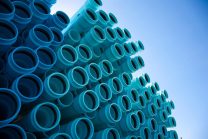
The Economic Impact of Rigid PVC Lubricant Systems
Lubricants are at the center of rigid PVC processing. They are the tools used to tune a rigid PVC compound to the processing equipment, and, if necessary, adjust for variations in other raw materials or changes in equipment conditions.
Lubricants affect the amount of work imparted into rigid PVC during processing, and influence where and when that work takes place in the processing equipment. In some ways lubricants can be thought of as inside material temperature and pressure controls which work in concert with outside equipment process controls (screw speed, orifice selection, and temperature profiles.)
The lubricant system itself is a relatively small part of the formulation costs for most rigid PVC operations. The only ingredient less expensive then lubricants in most rigid PVC formulations is calcium carbonate.
Lubricants impact the cost of goods sold on three different levels:
- Raw material cost
- Finished product dimensional tolerances
- Conversion costs
As a result, the costs and benefits, or the economics, of lubricant systems are complicated.
The contribution to raw material costs of a paraffin wax-based lubricant system is relatively small as the lubricant is used at a low level and has the lowest density of any ingredient. Changes in lubricant system levels have small impacts on overall raw material costs. For example, a 12.5 percent increase in lubricant system level from 2.00 phr to 2.25 phr increases formulation cost only 0.05 cents per pound assuming a PVC resin cost of 50 cents per pound and a lubricant system cost of $1.00/ per pound. These costs take into account changes in product density resulting from the level changes.
The benefits of using higher levels, or the optimum level, of lubricants typically far outweigh any additional raw material costs resulting from optimizing the lubricant system or levels.
A well balanced lubricant system directly impacts the ability to maintain consistent product dimensional tolerances, often known as material usage. If an optimized lubricant system results in a material usage reduction of 0.5 percent, the raw material costs to produce a finished product will be about 0.26 cents per pound lower for a typical PVC pipe formulation given a PVC resin cost of 50 cents per pound, or five times the cost of a 12.5 percent increase in lubricant level
A well-balanced lubricant system also typically allows higher production rates and results in fewer rejects. If conversion costs for a rigid PVC operation averages 10 cents per pound, and if half those costs are fixed and half are variable, a 10 percent increase in production rates will reduce average conversion costs 0.50 cents per pound or ten times the cost of a 12.5 percent increase in lubricant level.
Clearly, the payback for optimizing rigid PVC lubricant systems far outweigh changes in the cost of the lubricant system or in the usage levels of lubricants. Optimizing rigid PVC lubricant systems is one of the most powerful tools available to rigid processors to reduce the finish product cost of rigid PVC products.